The old art of paper folding comes to the computerised rapid prototyping paradigm with Pepakura Designer. Also if you are creating geometric structure that wont fit in the 3dprinter build space or a complex box that is not the simple ones available at boxes.py then consider exporting your 3d design to Pepakura so it can make you a laser cutting file. Pepakura Designer supports the export in several file formats, including BMP, PNG, GIF, JPG, EPS, DXF, and PDF.

Pepakura Designer provides a simple and useful toolset for layout editing. The Move, Rotate, and Join/Disjoin Parts editing tools, and the Adding Flaps function makes this unfolding process very easy to use. You do require a 3D model before starting to use Pepakura, and it supports common 3DCG and obj file formats from Rhino, blender, maya etc. As long as it has a low polygon count it should be easy to assemble.
I use it a lot for my LED art and festival events. For Ignition festival I designed a set of 3 animal masks for each of the tribes as part of the 2021 Pest Control Theme.
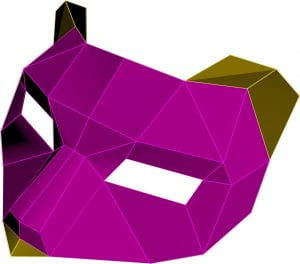
Rat mask 3d Model made in 3dsMax
After feeling happy with the designs I made in 3DsMax, I extracted the paper plan with Pepakura and laser cut it out. To complete this step I had to import the svg files into Illustrator and convert the lines into the correct colour and line type for laser cutting. (which can be fast is you use the select by appearance function). After cutting and assembling there would be changes after testing by wearing and handling the physical object, then making adjustments back in the 3Dmodel. After about 4 iterations I was happy with the design and sent the plans out to the festival precipitants so they could print out the plans on an A4 printer and build their own. As well as the human sized masks I build a huge version to stay in the lab for experimenting with projection mapping. As well as this big mask we make 3 GIANT versions in a barn on the Matamata festival site. To enlarge the design we projected the A4 plan through a roof mounted projector onto big fridge and bike boxes. Then we would assemble these together and cut lengths of aluminium LED diffuser channels to tape to the edges of the cardboard shape. After fastening all the aluminium together the cardboard was removed and smart pixel led strip lights installed in each channel.